ボンデ処理とは、金属製品の防錆性や耐久性を高めるための重要な表面処理技術です。この技術は、金属表面にリン酸塩皮膜を形成し、塗装の密着性を向上させるとともに、耐食性を強化します。
この処理では、金属表面にリン酸塩皮膜を作り、塗装の密着性をしっかり高めながら、耐食性もアップさせます。
特に、自動車部品や建築資材のように、頑丈さが求められる分野で大活躍しているんですよ。
矢内精工(株)のように、冷間鍛造や高精度な加工技術を提供する企業でも、製品品質をさらに高めるために、ボンデ処理のような表面処理技術を検討することがあるかもしれません。
「ボンデ処理とはどんな効果があるのだろう?」と気になる方もいるのでは? 一度ご検討いただくことで、製造効率アップや品質向上など、新たな可能性が見えてくるかもしれません!
この記事では、ボンデ処理の基本から、導入することで得られる企業メリット、さらに冷間鍛造との関係性までを、わかりやすく解説していきますので、ぜひ参考にしてくださいね!
ボンデ処理とは?冷間鍛造で欠かせない表面処理の重要性
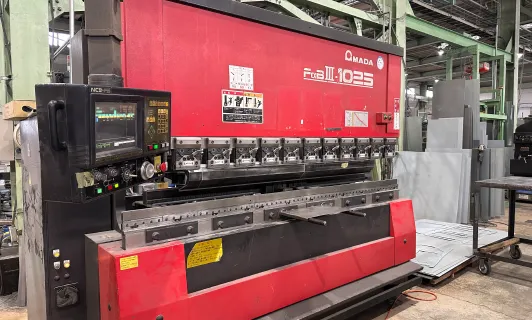
ボンデ処理とは、特に冷間鍛造のような金属加工工程で欠かせない表面処理技術です。
冷間鍛造の現場でこんな悩みはありませんか?
「金型がすぐに摩耗してしまう」「生産効率をもっと上げたい」と感じたことはないでしょうか?
こうした課題に答える技術が ボンデ処理 です!
金属成形の際に起こる摩擦やカジリ(接触による摩耗)は、生産ラインの効率や金型の寿命を大きく左右します。そこで登場するのが、金型表面に特殊なコーティングや皮膜を施すボンデ処理。
この処理により、耐摩耗性や耐熱性が向上し、金型の寿命を延ばすことができます。
冷間鍛造を行う企業にとって、ボンデ処理は高品質な製品を効率的に生産するために欠かせない存在です。以下では、ボンデ処理の特性や冷間鍛造における具体的な役割について、わかりやすく説明します!
ボンデ処理の概要と冷間鍛造における役割

ボンデ処理とは、金属表面にリン酸塩皮膜を生成し、その上に金属石けんを付着させる化成処理技術です。この処理により、以下のような特性が得られます。
- 金型の摩耗軽減:リン酸塩皮膜が金属間の直接接触を防ぎ、金型寿命を延ばします。
- 作業効率の向上:加工中の摩擦を軽減し、次工程でのプレスや圧造がスムーズになります。
冷間鍛造では、ボンデ処理が金型と金属素材の摩擦を抑え、カジリ(摩擦熱で表面が溶けて溶着する現象)を防ぐ重要な役割を果たします。
この処理により金型や工具の損傷を軽減し、交換や修理の頻度を抑えることで、製造工程の安定性と生産の効率が向上するでしょう。
結果として、カジリを防ぐことは、製品品質の向上、コスト削減、そして工程管理の最適化につながります。
ボンデ処理の利点と冷間鍛造への適用例
「金型がすぐ摩耗して困る…」「もっと効率的に作業を進めたい!」そんな悩みを抱える企業の担当者の皆さんに朗報です。冷間鍛造におけるボンデ処理には、こんな素晴らしい利点があります。
摩擦軽減で金型の寿命が延びる!
ボンデ処理とは、金型表面にリン酸塩皮膜を形成することで、摩擦を軽減し、金属同士の接触を抑える技術です。この処理により、金型の寿命が延び、生産効率の向上が期待できます。
大きな変形にも対応する柔軟性
金属素材が大きく変形しても、リン酸塩皮膜はしっかり密着したまま。これにより、金属表面が常に保護されるため、製品品質が安定します。「変形が多い工程でも安心して使える」そんな信頼感があります。
潤滑性がアップして作業がスムーズに!
ボンデ処理の仕上げに使われる金属石けんが潤滑層を形成します。この潤滑層のおかげで、冷間鍛造の際に発生する圧力や熱にも耐えながら、滑らかな作業が可能になります。これで生産効率もグンと向上しますよ!
冷間鍛造における環境対応型潤滑剤の可能性

「でも、ボンデ処理って環境に悪いのでは?」
確かに、化学薬品の使用や廃液処理の問題、さらにはエネルギー消費が多いことなどが理由で、環境への影響を心配される方もいるでしょう。
ただし、最近では環境負荷を軽減するための技術や取り組みも進んでおり、より持続可能な方法でボンデ処理を行うことが可能になってきています。
実際、化学的処理に伴う廃水や廃棄物の発生は課題の一つです。これを解決するために、近年注目されているのが 環境対応型潤滑剤 です。
この新しい技術は、塗布と乾燥だけで完了するシンプルな処理で、環境負荷を大幅に軽減します。複雑な工程を必要としないため、生産効率もアップ!
まだ開発段階ではありますが、「環境にも優しく、生産効率も上がる」この技術が、将来的にボンデ処理を補完する重要な存在になることが期待されています。
ボンデ処理の具体的な工程とその仕組み
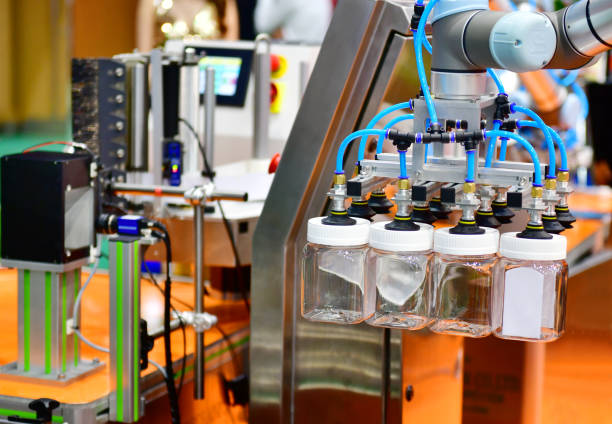
「ボンデ処理とは、金属製品の防錆性や耐久性を高める重要な技術ですが、実際にはどのように行われるのか気になりますよね?」そんな疑問をお持ちの方のために、ここではボンデ処理の基本的な工程をわかりやすくご紹介します!
- 金属表面の準備(ショットブラストや酸洗)
金属表面の汚れや酸化皮膜を取り除き、化成処理がしやすい状態にします。 - リン酸塩皮膜の形成
リン酸溶液に金属を浸漬し、表面に保護皮膜を形成。この皮膜が金属を錆びから守るだけでなく、塗装密着性を高めます。 - 金属石けんの付着(潤滑層の形成)
皮膜の上に金属石けんを付着させることで、滑り性を向上。冷間鍛造時の摩擦を低減します。
これらの工程がスムーズに行われることで、金型寿命の延長や作業効率の向上が実現します!
他の表面処理との違い:どれを選ぶべき?
「ボンデ処理とは?他の技術、何が違うの?」という疑問にお答えします。以下の処理と比較して、ボンデ処理の特徴を見てみましょう。
ガルバリウム鋼板との違い
ガルバリウム鋼板は、金属の耐食性を高めるために亜鉛、アルミニウム、シリコンの合金メッキが施された鋼板です。
この特性により、ガルバリウム鋼板は錆びにくく、耐久性の高い材料として広く利用されています。
一方で、塗装密着性という観点では、ボンデ処理に比べて劣る場合があります。
ボンデ処理では、金属表面に形成されるリン酸塩皮膜が塗料の密着を強化し、塗装剥がれを防ぐ効果があるため、塗装が重要な製品にはボンデ処理が適していると言えるでしょう。
亜鉛メッキとの違い
亜鉛メッキは、金属表面に亜鉛の層を付着させることで防錆性を高める処理方法です。そのシンプルな工程と比較的低いコストが大きな利点となっています。
しかし、ボンデ処理と比較すると、摩擦軽減や加工性の向上といった点では劣ります。特に、冷間鍛造など高い潤滑性が求められる工程では、ボンデ処理のリン酸塩皮膜と金属石けんによる潤滑効果が非常に重要です。
このため、亜鉛メッキはコスト面でのメリットが大きく、予算を重視する場合に適した選択肢です。一方で、性能面での総合力や高い耐久性を求める場合には、ボンデ処理がより適していると言えるでしょう。
ボンデ処理のコスト
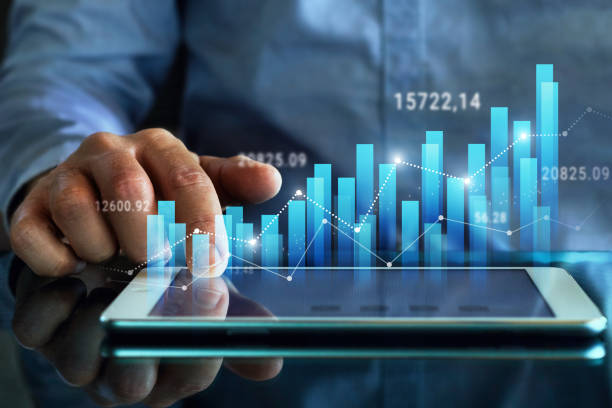
ボンデ処理を導入しようと考えると、「初期投資や運用コストってどのくらいかかるのだろう?」と気になりますよね?ここでは、導入を検討する際に知っておきたいコスト構造と注意点について、わかりやすく解説します!
ボンデ処理:設備投資コスト
ボンデ処理には、ショットブラストやアルカリ脱脂、酸洗、リン酸塩皮膜の形成など多くの工程を処理する設備が必要です。そのため、初期投資が高額になる点が課題です。「長く使えるけど、導入時の負担が大きい」と感じる方も多いでしょう。
ボンデ処理:ランニングコスト
薬品費やエネルギー消費に加え、廃液やスラッジ処理費用が発生します。特に、月に8トンものスラッジが出る場合もあり、適切な管理が必要です。
ボンデ処理:メンテナンスと管理
設備のメンテナンスや薬品の補充には、人手が必要です。さらに、環境法規制に対応する排水処理設備の運用費用もランニングコストに含まれます。
ボンデ処理の導入時の注意点
「ボンデ処理を導入する際、どんなことに気をつければいいの?」そんな疑問をお持ちではありませんか?
ここでは、環境配慮やコスト対策など、導入時に押さえておきたいポイントを簡潔にご説明します。
環境負荷の軽減対策
ボンデ処理ではリン酸塩や重金属を含む廃液が発生します。
そのため、環境対応型潤滑剤を採用すれば、排水処理のコスト削減と環境負荷の軽減が実現します。
工程の簡素化
「ボンデ処理は多くの工程があり、時間がかかるのがネック…」と感じる方もいるでしょう。
最近では「一液型潤滑剤」や「環境対応型潤滑剤」を導入することで、工程数の削減や処理時間の短縮が期待されています。
コスト対効果とは?導入時に注目すべきポイント
新技術の採用で設備コストが約3分の1、ランニングコストが半分に削減されるケースも。
導入前にコストと効果をしっかり比較検討しましょう。
新技術の導入検討
最近注目される「環境対応型潤滑剤」は、廃液削減やエネルギー消費の低減が可能です。特にグローバル展開を目指す企業にとって有効ですが、用途や性能要求を見極めた慎重な判断が必要です。
ここでの内容は、以下の文献を参考にしています。詳細についてはこちらをご覧ください。
まとめ
ボンデ処理とは、製品の防錆性や耐久性を高め、工程の効率化にも影響する重要な技術です。一方で、コストや環境負荷の課題もあり、導入には慎重な検討が必要ですよ!
矢内精工(株)では、冷間鍛造や高精度な加工技術を通じて、お客様のニーズに合った最適な製造プロセスをサポートしています。
表面処理技術の導入を含めた製造課題についてのご相談があれば、ぜひお気軽にお問い合わせください!