冷間鍛造は自動車部品の高精度・高耐久性を実現する重要な技術です。
自動車メーカーや部品メーカーにとって、冷間鍛造の技術を正しく理解することは、軽量で耐久性のある部品設計の鍵となります。
本記事では、冷間鍛造の基本や自動車部品におけるメリット、矢内精工(株)が提供する高品質な製品とサービスについて詳しくご紹介します。
冷間鍛造の特徴と自動車部品への適用
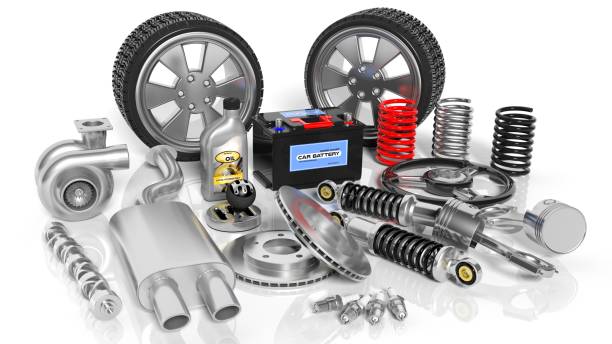
冷間鍛造とは、金属を加熱せず常温で高圧をかけて成形する技術です。
この方法は、特に高い寸法精度と滑らかな表面仕上げが特徴です。
一方で、一般的な鍛造(熱間鍛造)は、金属を加熱して柔らかくするため、冷間鍛造より精度がやや劣ることがあります。
このような特徴から、冷間鍛造は自動車部品の製造に多くのメリットをもたらし、特に複雑な形状や高精度が求められる部品の製造に最適です。
冷間鍛造によって得られる具体的なメリットは次の通りです。
- 追加の機械加工が不要:高精度で加工されるため、後加工の手間がほぼ不要になる。
- 材料の無駄を削減:効率的に成形できるため、材料の使用量が最小限で済む。
- 自動化に適している:工程の自動化が容易で、生産性が向上。
- 複雑な形状にも対応可能:複数の工程を組み合わせ、複雑な形状の部品も効率よく作れる。
これらの特性により、冷間鍛造は自動車産業において、ボルトやナット、トランスミッションのギア、シャフト、ボールジョイントなどの大量生産が求められる部品の製造に不可欠な技術です。
自動車部品における冷間鍛造のメリット
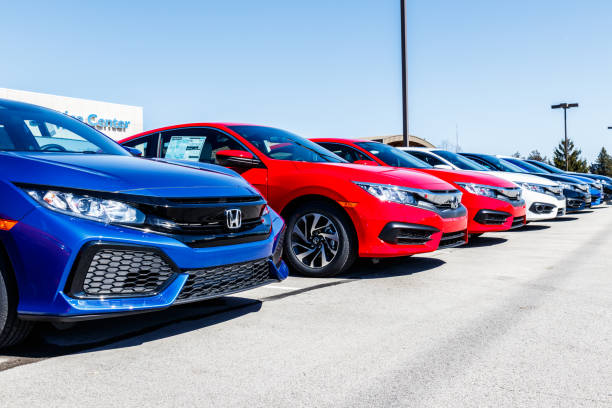
冷間鍛造は、自動車部品の製造において欠かせない技術です。
具体的には、高精度・高耐久性・環境負荷の低減など、業界の多様なニーズに応えます。
まず、冷間鍛造技術により、金属の強度向上や寸法の安定性が実現されるため、自動車メーカーは信頼性の高い部品を安定的に供給でき、品質向上にもつながります。
また、加工のばらつきが少ないため、同じ精度の部品を大量生産でき、コスト削減や生産速度の向上にも貢献。
この技術により、自動車メーカーは短納期での部品調達が可能となり、サプライチェーン全体の効率化も図れます。
さらに、冷間鍛造は軽量金属の加工にも適しており、車両の燃費向上やコスト削減にも寄与します。
このため、エコロジーを重視した次世代の車両製造においても、重要な役割を果たしています。
強度と精度の向上
冷間鍛造は、金属を常温で高圧力で成形するため、内部の金属粒子が圧縮され、隙間のない緻密な構造が形成されます。
この技術により、金属の強度と寸法精度が向上し、耐久性が特に求められる自動車部品に最適です。
自動車部品は激しい振動や衝撃に耐える必要があるため、強度が高く寸法精度が安定していることが重要です。
冷間鍛造を活用することで、エンジンやトランスミッションなど精密さが求められる部品も効率的に製造できます。
安定した高品質部品の供給
冷間鍛造は、金属を常温で高圧力で成形するため、加工時の寸法変動が少なく、高精度の部品を大量に安定供給できます。
この特性により、自動車の製造ラインで高品質な部品を安定的に供給することが可能です。
さらに、後加工の工程が少ないため、生産効率が向上し、コスト削減にも貢献します。
冷間鍛造による量産性の向上は、予算内での部品供給を実現し、自動車メーカーが信頼性の高い車両を提供するための大きな強みとなります。
燃費向上と軽量化の促進
現在では、車両の燃費向上や環境負荷低減のため、軽量化が重要視されています。
冷間鍛造は、アルミニウム合金やマグネシウム合金などの軽量金属に対応し、車両の軽量化に大きく貢献。
その結果、燃費性能の向上と環境負荷の低減が期待されています。
幅広い部品の製造への対応
冷間鍛造は、エンジン部品(ピストンやコンロッド)、トランスミッション部品、ステアリング部品、サスペンション部品など、多種多様な自動車部品の製造に活用されています。
特に、エンジン内部のような高い強度と耐熱性が必要な部品において、その特性が効果的に発揮されます。
環境にやさしい冷間鍛造の貢献
冷間鍛造は、自動車業界において環境負荷の軽減に貢献する技術です。
エネルギー効率が高く、従来の熱間鍛造と比べて二酸化炭素の排出量を抑えることができます。
また、冷間鍛造は材料の利用効率が高いため、資源の無駄を減らし、製造過程での廃棄物削減にも役立ちます。
こうした特性により、地球環境に配慮した持続可能な製品作りを可能にする加工方法として注目されています。
冷間鍛造は自動車産業に欠かせない加工技術
冷間鍛造は、自動車部品の「性能向上」「安全性確保」「環境負荷低減」に応える重要な技術です。
高精度な部品製造を可能にし、軽量化や耐久性向上にも貢献します。
この技術により作られる部品は、自動車の安全性と性能を支え、持続可能な製造方法として注目されています。
自動車部品に求められる矢内精工の冷間鍛造の強み
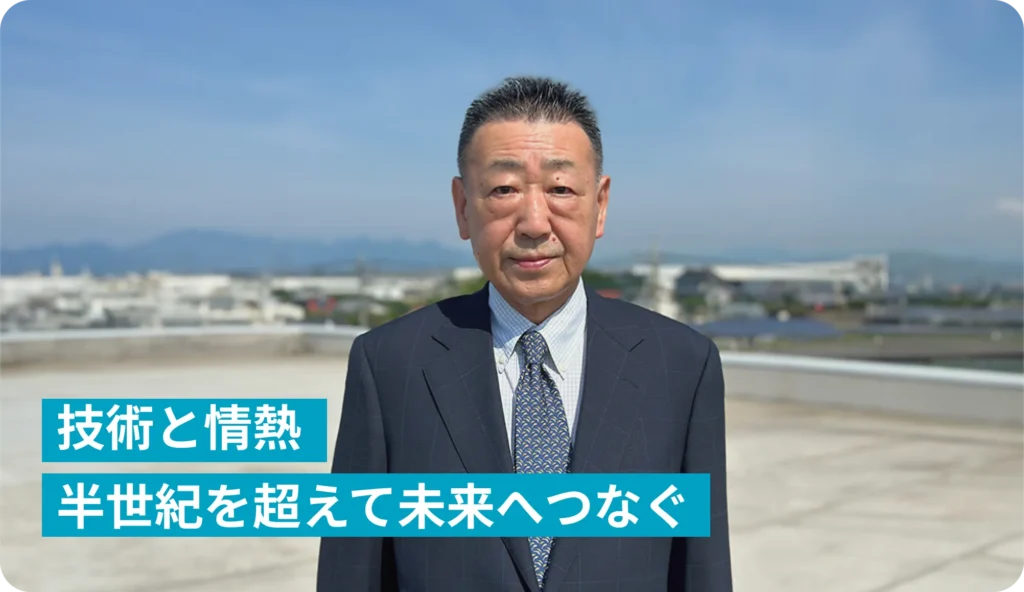
矢内精工(株)の強みは、熟練職人の技術と最新の自動化技術がうまく融合している点です。
同社では、経験豊富な技術者が精密な加工を行い、同時に最新の自動化技術を取り入れることで、安定した品質と高い精度の製品を提供しています。
これにより、自動車部品に求められる高い信頼性を確保し、品質にこだわるお客様のニーズに応えています。
高精度検査と品質管理
矢内精工(株)では、全製造ラインで厳密な品質検査を行い、一貫した品質管理体制を整えています。
ISO9001の認証を取得しており、国際基準に基づいた品質管理のもとで製品を提供。
これにより、常に高い品質を保っています。
また、品質方針は定期的に見直し、更新することで、顧客の期待に応える製品づくりに努めています。
さらに、必要に応じて第三者機関による検査にも対応しており、納品後も安心して使っていただける品質を保証しています。
矢内精工が製造する冷間鍛造自動車部品の例
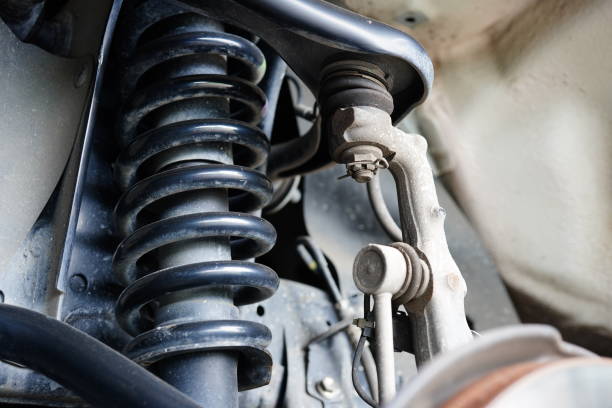
冷間鍛造は、自動車部品製造において欠かせない技術です。
この技術により、高精度で高強度な部品が効率的に製造され、多くの自動車部品に活用されています。
矢内精工(株)では、熟練の技術と最新設備を活かし、高品質な冷間鍛造部品を提供しています。
サスペンション部品
車両の安定性や乗り心地に重要なサスペンション部品も、冷間鍛造技術の利点が活かされています。
矢内精工(株)の冷間鍛造技術により、サスペンション部品に求められる高い精度と強度が実現され、寸法の安定性や長期間の耐久性が確保されています。
このような高品質な足回り部品は、自動車メーカーからの厚い信頼を得ており、信頼性と安全性の高い製品を提供し続けています。
冷間鍛造のサイズのばらつき管理と精度!矢内精工の取り組み
冷間鍛造技術は、自動車部品製造において高精度で信頼性のある製品を実現するために不可欠です。
特に、サイズのばらつき管理は、製品品質を保つうえで重要な要素となります。
矢内精工(株)では、長年の経験と最新の品質管理システムを駆使し、冷間鍛造部品のサイズのばらつきを厳密に管理しています。
冷間鍛造のサイズのばらつき管理の重要性
- 冷間鍛造部品には、非常に高いサイズ精度が求められる。
- 矢内精工(株)では、JIS規格に基づき、業界基準以上の精度で部品を提供するため、厳密なサイズ管理を行っている。
これにより、信頼性の高い部品を安定的に供給できる体制を確立しています。
品質保証と検査体制
- 矢内精工(株)では、製造工程での抜き取り検査や製品検査を定期的に行い、寸法精度を徹底的に確認。
- 厳格な品質管理体制のもとで、常に高精度な部品を提供し、自動車業界における高い信頼性を確保。
自動車部品における矢内精工の冷間鍛造技術:実績と未来展望
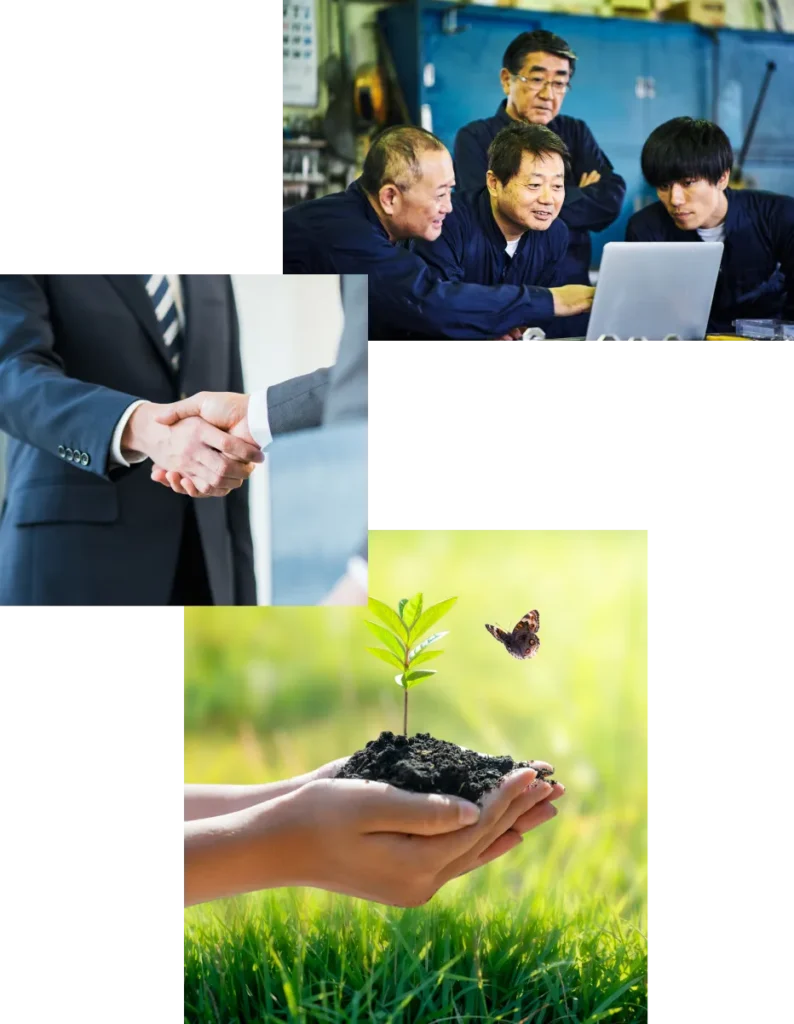
矢内精工(株)は、冷間鍛造技術を活用し、自動車部品を高精度かつ高品質に製造しています。
特に、カーエアコン用コンプレッサーのリンクアームやシリンダー部品の加工技術を確立し、品質と生産性の向上を達成。
また、専用機の導入により、自動車用アルミニウム部品の寸法精度が向上し、後工程の効率化も実現しています。
こうした取り組みにより、日本国内外の自動車メーカーから信頼されるパートナーとして、多様な部品を安定的に供給しています。
今後も冷間鍛造技術をさらに革新し、複雑な形状や高強度が求められる自動車部品の製造技術を強化することで、自動車産業をはじめ幅広い分野への貢献を目指します。
Q&A:冷間鍛造と自動車部品に関するよくある質問
Q1:冷間鍛造の寸法公差はどのように管理されていますか?
A1:矢内精工(株)では、JIS規格(日本工業規格)に基づき、厳密な寸法公差管理を行っています。製造工程中の抜き取り検査と製品検査で高精度な部品を保証しています。
Q2:冷間鍛造部品は自動車のどの部分に使用されていますか?
A2:エンジンやサスペンション、シャーシなど、強度と耐久性が求められる部品に使用されています。
Q3:冷間鍛造製品の量産期間はどれくらいですか?
A3:製品の仕様にもよりますが、通常は2〜3ヶ月程度です。
まとめ:冷間鍛造で実現する高品質な自動車部品製造
冷間鍛造は、自動車部品の強度と精度を高め、環境に配慮した製造方法として、今後ますます注目される技術です。
矢内精工(株)は、長年にわたる経験と最新技術を融合し、信頼性の高い自動車部品を国内外の自動車メーカーに提供しています。
もし高精度で耐久性に優れた自動車部品をご検討中なら、ぜひ矢内精工(株の冷間鍛造技術をご確認ください。
品質を最優先する企業様へ、安心してお任せいただける製品をお届けいたします。
詳細なご相談やお問い合わせは、公式サイトのお問い合わせコーナーよりお気軽にどうぞ。