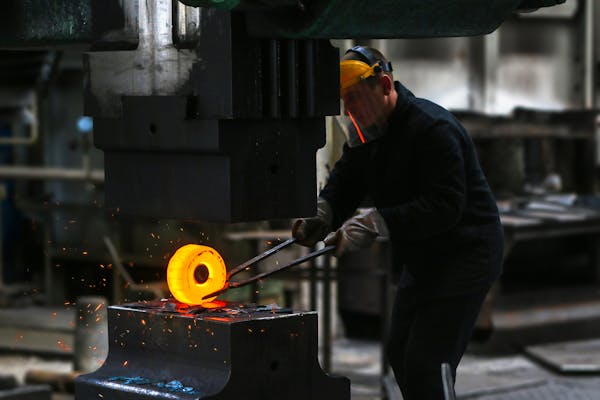
冷間鍛造(Cold Forging)は、強度と精度を両立しながらエネルギーコストを削減できる技術として、製造業に革命をもたらしています。
特に、自動車部品や産業機械の製造で、その高効率かつサステナブルなプロセスが注目されています。
冷間鍛造の工程と特徴
冷間鍛造は、金属を加熱せずに常温で圧力を加え、変形させながら目的の形に成型する加工方法です。
この技術は、精密さと効率性を兼ね備えた金属加工法であり、特に高精度な製品や複雑な形状が必要な場合に最適です。
冷間鍛造の基本的な工程と特徴をわかりやすく説明します。
常温での加工
- 常温のままで金属に圧力を加えること
- 結晶構造を保ちながら強度と精度を高めて成型できる
冷間鍛造の最大の特徴は、常温のままで金属に圧力を加えることです。
通常の熱間鍛造では金属を高温に加熱して柔らかくしてから成型しますが、冷間鍛造では加熱が不要です。
これにより、金属の結晶構造を保ったまま加工でき、材料の強度や精度が非常に高い状態で成型されることが大きな利点となります。
高精度な成型
- 寸法精度が非常に高い
- 仕上げ加工が不要なこともある
冷間鍛造では、寸法精度が非常に高いため、複雑な形状や細かいディテールを必要とする部品にも対応可能です。
さらに、仕上げ加工が不要なこともあるため、自動車部品や精密機械の部品など、寸法に厳しい製品に多くの産業で採用されています。
材料の無駄が少ない
- 材料の無駄がほとんどない
- コスト削減につながるメリット
冷間鍛造では、材料の無駄がほとんどないため、削り屑や廃棄物が少なく済みます。
その結果、材料費を抑えられ、コスト削減につながるメリットがあります。
高速加工
- 毎分100個前後の高速加工が可能
- 複雑な形状も高い精度で成型できる
冷間鍛造は、毎分100個前後の高速加工が可能であり、大量生産が求められる製品にも対応できます。
さらに、複雑な形状も高い精度で成型できるため、自動車部品や産業機械部品の製造に大きなメリットがあります。
強度と耐久性の向上
- 加工硬化によって強度が増す
- 高い耐久性を持ち、長期間使用できる品質を提供
冷間鍛造では、加工硬化によって強度が増すため、製造された部品は高い耐久性を持ち、長期間使用できる品質を提供します。
これにより、自動車のエンジン部品や耐久性が求められる機械部品に特に適しています。
冷間鍛造の技術的な優位性
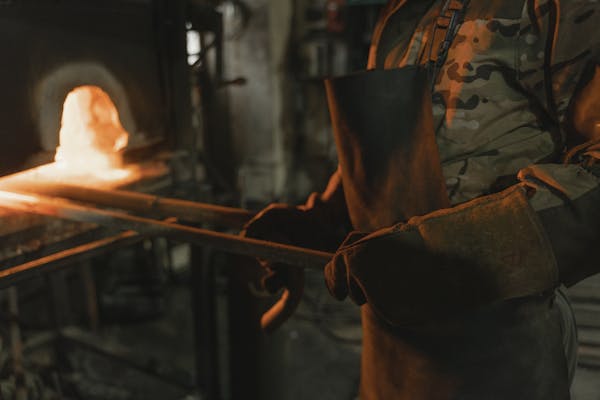
冷間鍛造は、常温で金属を成形する高度な技術であり、さまざまな製造業において多大なメリットをもたらしています。
この技術が持つ強みは、高精度な加工とコスト効率の向上です。
以下に、冷間鍛造の技術的な優位性についてわかりやすく解説します。
高い寸法精度
冷間鍛造は常温で金属を加工するため、金属の膨張や収縮が発生せず、非常に高い寸法精度を実現できます。
この技術により、複雑な形状や微細なディテールを高精度で成形できるため、自動車部品や航空機のエンジン部品など、厳しい寸法管理が求められる製品に最適です。
熱を加えないことで、最終製品の仕上がりも向上し、追加の仕上げ加工が不要な場合もあります。
材料の無駄が少ない
冷間鍛造では、金属を削り取るのではなく、圧力を加えて形状を作り上げます。
これにより、材料の削り屑や廃棄物がほとんど発生しないため、製造過程での無駄が少なく済みます。
この点は、資源の無駄を省きつつ、材料費を削減し、コスト効率を高める大きなメリットです。
また、エコフレンドリーな技術としても評価されています。
高速加工能力
冷間鍛造は、毎分100個前後の高速加工が可能です。
この生産速度の速さは、大量生産が求められる自動車産業や工業製品において非常に有用です。
高速でありながらも、製品の精度を保ちながら複雑な形状の部品を作ることができるため、効率と品質の両立が求められる現代の製造業にとって重要な技術です。
強度と耐久性の向上
- 金属に圧力を加えることで、素材内部の結晶構造が変化し、強度が高まる
- 冷間鍛造された部品は、より高い強度と耐久性を持つ製品となり、長期間にわたって使用できる
金属に圧力を加えることで、素材内部の結晶構造が変化し、強度が高まるため、成型された部品は通常よりも頑丈になります。
さらに、冷間鍛造された部品は、より高い強度と耐久性を持つ製品となり、長期間にわたって使用できるため、特に耐久性が重要な製品に適しています。
環境に優しいプロセス
冷間鍛造は、金属を加熱せずに加工するため、エネルギー消費が少なく、環境への負荷が低いプロセスです。
製造工程において廃棄物もほとんど発生しないため、環境に配慮した製造技術として、持続可能な製造を目指す企業にとって理想的な選択肢となります。
冷間鍛造の優位性は、高精度、コスト効率、耐久性の向上、そして環境への配慮にあります。
この技術がもたらす多くの利点は、さまざまな産業で重宝され、自動車や航空機部品の製造をはじめとする、厳しい基準が求められる製品に特に適しています。
冷間鍛造と熱間鍛造の違い
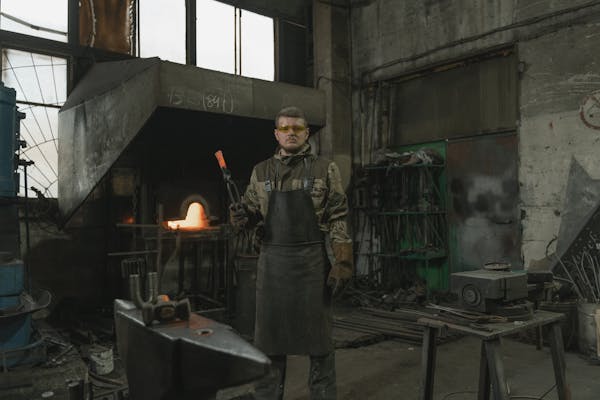
冷間鍛造と熱間鍛造は、金属加工における重要な技術であり、それぞれの特長とメリットが異なります。
ここでは、どのようにこの2つの鍛造技術が異なり、どのような状況でどちらを選ぶべきかをわかりやすく説明します。
金属の加工温度が異なる
- 冷間鍛造は、金属を常温で加工するため、寸法精度が非常に高く、表面の仕上がりが優れています。
- 熱間鍛造は、金属を高温で加熱してから加工するため、金属が柔らかくなり、複雑な形状や大型部品の成形に適しています。
表面仕上がりと精度
冷間鍛造の利点は、表面の仕上がりが非常に綺麗で、寸法や形状の精度が高いことです。
例えば、自動車部品や精密機械の部品など、細部の精度が必要な製品に向いています。
一方、熱間鍛造では、表面が粗くなることがあり、後工程での仕上げ加工が必要になる場合がありますが、大きな部品や複雑な形状の部品を成形するのに最適です。
成形力と材料の特性
冷間鍛造は、常温で硬い金属を成形するため、大きな圧力が必要です。
したがって、金属に負荷がかかりやすく、製品が割れるリスクや金型への負担が増します。
熱間鍛造では、金属が柔らかい状態で加工するため、複雑な形状や大きな部品でも比較的容易に成形できます。
金属が割れるリスクも低いため、大型部品や高強度部品の製造に適しています。
適用される製品の違い
冷間鍛造は、小型部品や精度が重視される製品に向いています。
自動車のエンジン部品や産業機械の精密部品など、高い強度と精度を求める製品に最適です。
熱間鍛造は、複雑な形状や大型の部品の製造に適しています。
たとえば、建設機械や船舶の部品、さらには航空機の構造部材など、頑丈で大きなサイズの製品が求められる分野で利用されています。
【冷間鍛造と熱間鍛造の比較表】
特徴 | 冷間鍛造 | 熱間鍛造 |
---|---|---|
表面の仕上がり | ◎ 綺麗 | ○ 仕上げが必要 |
寸法・形状精度 | ◎ 高い精度 | ○ 良好 |
ロット対応 | 大ロット向き | 大中ロット対応 |
複雑形状の成形 | ○ 可能 | ◎ 最適 |
大型部品の成形 | × 不向き | ◎ 最適 |
矢内精工の冷間鍛造技術
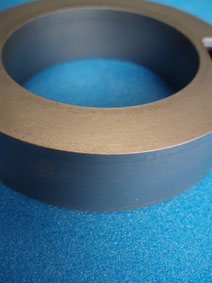
矢内精工(株)の冷間鍛造技術は、高精度かつ高品質な製品を提供するため、特に自動車や産業機械の部品製造で強みを発揮しています。
独自の金型設計技術を駆使し、複雑な形状や特殊な要求に対応可能です。
さらに、厳密な品質管理体制により、精度と耐久性の高い製品を提供し、クライアントの生産効率向上に寄与しています。
これらの技術力は、製品の高い信頼性を支えています。
冷間鍛造の適用分野と実績
矢内精工(株)の冷間鍛造技術は、自動車、航空宇宙、精密機器など幅広い産業に活用されており、高精度と高強度を提供することが強みです。
特に、自動車のエンジン部品や航空機の軽量高強度部品、精密機器の小型高精度部品に最適です。
これにより、車両の安全性向上やエネルギー効率の高い製造が実現し、長期的なコスト削減も期待できます。
冷間鍛造の市場動向と今後の展望
冷間鍛造の市場は、自動車や航空宇宙産業を中心に軽量・高強度部品の需要が増加しています。
特に電気自動車(EV)の普及が進む中、冷間鍛造技術が不可欠です。
技術の進化や自動化、コンピュータ支援製造により、効率と精度が向上し、さらに普及が進む見込みです。
また、材料効率の高さがコスト削減に寄与し、新興国の工業化や製造活動の増加が市場を後押ししています。
今後、冷間鍛造はより多くの産業で活用され、部品の高性能化と耐久性向上に貢献するでしょう。
矢内精工が提供する冷間鍛造で競争力アップ!
矢内精工(株)の冷間鍛造技術は、高精度な製品製造とコスト削減を両立する画期的な技術です。
自動車や航空宇宙産業など、高強度と耐久性が求められる部品を製造する企業にとって理想的な選択肢です。
環境負荷の少ないサステナブルな製造方法で、企業の競争力を高めることができます。
今すぐお問い合わせいただき、貴社の製造プロセスにこの技術を導入して、さらなる効率化と品質向上を目指しましょう。