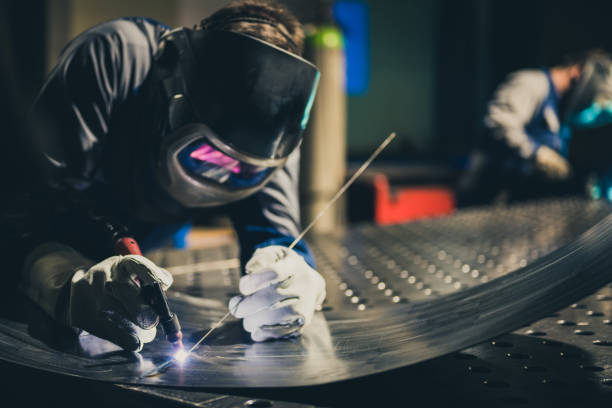
溶接における注意点として、安全対策の徹底や適切な技術の使用が重要です。
これにより、製品の品質を保ち、作業者の安全も守れます。
溶接作業は一見シンプルに思われがちですが、実際にはさまざまなリスクが潜んでいます。
ちょっとしたミスが大きな事故や製品の不具合につながることも。
では、どうすれば安全かつ高品質な溶接を実現できるのでしょうか?
今回は、溶接の基本から現場で使えるプロのテクニックまで、知っておくべきポイントを分かりやすくお伝えします!
溶接作業の重要性とその注意点
溶接は、金属同士を一体化させるための重要な工程です。
特に、自動車の製造やバルブの接合、建築用鉄骨の組み立てなど、さまざまな産業で広く使用されています。
溶接の質が高いほど、製品の安全性や耐久性が向上し、長期にわたりその機能を果たすことが可能です。
しかし、溶接作業には多くのリスクや課題が伴います。
ここでは、アーク溶接作業における主な注意点とその対策について詳しく解説し、品質と安全性を確保するための最適なアプローチを紹介します。
アーク溶接の基礎知識と注意点

アーク溶接は、金属同士を強固に接合するための溶接方法です。
電気アークの熱を利用して金属を溶融し、冷却して接合します。
この方法は、多くの利点を持つ反面、高温や紫外線、スパッタ(溶融金属の飛び散り)などの危険性も伴います。
防護具の重要性
アーク溶接作業中は、強い紫外線や火花が発生。
これにより、火傷や眼の損傷といったリスクが生じます。
作業者は必ず耐火性のある作業服、溶接用手袋、保護メガネ、そして溶接マスクを着用し、安全対策を徹底する必要があります!
換気とガス管理
アーク溶接では、有害な煙やガスが出ることがあります。
これらのガスを吸い込むと、健康被害を引き起こす可能性があるため、作業場の換気を十分に行い、健康を守るためのガス管理が必要です。
特にガスシールド溶接の場合は、使用するガスの種類や濃度にも注意を払う必要があります。
電気ショックの防止策
高電圧を使用するアーク溶接では、電気ショックのリスクも伴います。
湿度が高い環境では、感電のリスクがさらに高まるため、絶縁手袋や安全靴を使用し、溶接機器の絶縁状態を定期的に確認することが必要です。
高張力鋼の溶接!強度を最大化するための注意点

高張力鋼は、自動車や建築構造物での使用が一般的で、その高い引張強度と耐衝撃性から軽量化が求められる構造物に使われます。
しかし、その溶接には特別な注意が必要です。
適切な温度管理
高張力鋼の溶接には、過熱や冷却速度の制御が重要です。
過度な熱が加わると、素材の靭性が低下するため、事前に適切な予熱を行い、溶接後の冷却速度を調整することで、最適な強度を維持できます。
溶接材の選択
使用する溶接材は、母材と同等以上の強度を持つものを選ぶことが必要です。
これにより、溶接部が他の部分よりも弱くなるリスクを防ぐことができます。
バルブ溶接の注意点!漏れを防ぐための対策
バルブは、液体やガスの流れを調整・制御するための重要な部品です。
バルブの溶接部分に小さな隙間が生じると、そこから液体やガスが漏れる可能性があります。
こうした漏れが発生すると、システム全体の機能が低下し、安全性に大きなリスクをもたらすことになります。
特に、高圧環境や危険物を扱うシステムでは、漏れが大きな事故や故障の原因になることもあるので、十分な注意が必要です。
バルブの溶接作業では、こうした漏れを防ぐために、非常に細かく丁寧な作業が求められます。
わずかな隙間でも液体やガスが漏れる可能性があるため、溶接では金属同士をしっかり接合し、隙間が全くできないように注意する必要があります。
したがって、バルブ溶接には高い技術力と正確な作業が不可欠です。
これにより、漏れのリスクを最小限に抑え、システム全体の安全性と信頼性を維持できます。
精密な溶接
微小な隙間を避けるためには、TIG溶接のような高精度な溶接方法が効果的です。
TIG溶接では、タングステン電極を使用し、不活性ガスで溶接部分を保護するため、酸化が起こりにくく、非常に美しく正確な仕上がりが可能です。
また、熱の制御がしやすく、薄い金属や細かい部分の溶接に適しているため、精密な作業が求められる場面で多く採用されています。
このように、TIG溶接を使うことで、溶接部分の品質が向上し、長期間にわたって耐久性が保たれるでしょう。
溶接後のテスト
漏れを確認するためには、溶接後に圧力テストや漏れ試験を実施することが不可欠です。
これらのテストを行うことで、溶接部の品質と安全性を確保できます。
アルミ・ステンレスの溶接!酸化を防ぐための工夫

アルミやステンレスは、その特性上、酸化しやすいため、溶接作業には特別な工夫が必要です。
不活性ガスの使用
アルミやステンレスの溶接では、不活性ガス(例:アルゴンガス)を使用して酸化を防ぎます。
特に、TIG溶接では不活性ガスが保護シールドとして機能し、酸化の発生を抑えます。
清浄な表面
溶接前には、溶接面の酸化皮膜を完全に除去することが重要です。
これにより、より良好な溶接品質が得られ、接合部の強度が向上します。
自動車・トラックの溶接!安全性を確保するための注意点
自動車やトラックの溶接は、安全性を最優先に考えなければなりません。
溶接不良が事故の原因となる可能性があるため、溶接作業者は特に注意を払う必要があります。
高品質の溶接機器の使用
高品質な溶接機器を使うことで、以下のメリットがあります。
- 精密な制御: 各材料に合った温度や条件で溶接でき、強度と耐久性が保たれます。
- 多様な溶接法に対応: スポット、レーザー、MIGアーク溶接など、さまざまな方法に対応し、幅広い材料に対応可能です。
- 安定した品質: 溶接精度が向上し、常に一貫した高品質な仕上がりが得られます。
経験豊富な技術者による作業
自動車の溶接は高度な技術が求められるので、経験豊富な技術者による作業がおすすめです。
技術者の経験とスキルによって、溶接の精度や品質がアップし、安全性もきちんと守られますよ。
炭素鋼および鉄骨の溶接!構造強度を最大化する方法

建築用鉄骨や炭素鋼の溶接は、建物の安全性と耐久性に直結する重要な工程です。
特に、溶接部の強度不足やクラックが発生すると、耐震性にも深刻な影響を与える可能性があります。
溶接部の強度不足やクラックの発生は、建築物全体の安全性を左右するため、特に入念な検査と技術力が求められます。
適切な溶接手法の選択
鉄骨や炭素鋼の溶接には、アーク溶接が一般的です。
アーク溶接は深い溶け込みが可能で、強固な接合部を形成できます。
定期的な点検とメンテナンス
溶接後の定期的な点検とメンテナンスは、構造物の安全性を保つために非常に重要です。
特に、溶接部にひび割れや腐食がないかを定期的に確認することで、耐久性を確保し、長期的な安全性を維持することができます。
矢内精工株式会社の強みと取り組み
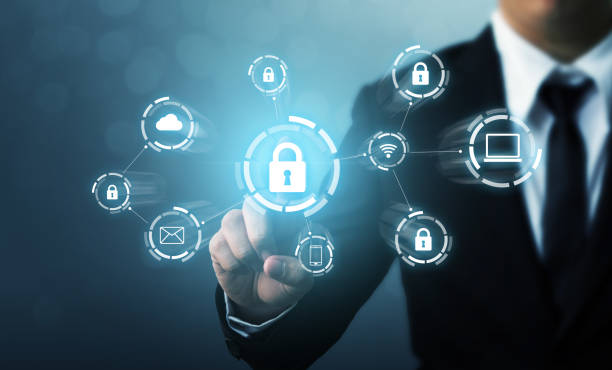
矢内精工(株)は、溶接分野において長年の経験と高い技術力を持ち、安全性と品質を最優先に考えたサービスを提供しています。
お客様のニーズに応えるため、最新の技術や設備を常に導入し、業界の最前線で対応しています。
高度な技術と設備の活用
矢内精工(株)は、最新の溶接技術を導入し、精度の高い作業を実現しています。
その結果、製品の品質をしっかりと維持し、お客様に信頼されるものづくりを続けています。
徹底した安全教育とリスク管理
溶接作業の安全性を守るために、全ての作業員に定期的な安全教育を行っています。
作業員がしっかりリスクを理解し、適切な安全対策を取ることで、事故を防ぐ取り組みを徹底しています。
顧客満足度の追求
私たちはお客様のニーズを最優先に考え、ベストな溶接ソリューションを提案しています。
アーク溶接の専門知識を持つスタッフが、プロジェクトの始めから終わりまでしっかりサポート。
お客様に満足いただけるよう、信頼関係を大切にしています。
よくある質問(FAQ)
Q1: アルミ溶接に特に注意すべき点は何ですか?
アルミ溶接では、酸化を防ぐために不活性ガス(アルゴンガス)の使用が重要です。
また、溶接前に酸化皮膜を徹底的に除去することも必要。
Q2: 自動車の溶接作業で特に注意すべき点は?
自動車の溶接では、高品質の溶接機器の使用と、経験豊富な技術者による作業が重要です。
また、適切な溶接手法を選ぶことで、強度と安全性を確保します。
Q3: 溶接作業の際に特に注意すべきことは何ですか?
溶接作業では、作業者の安全を確保するための防護具の着用と、作業場所の十分な換気が必要です。
特にアーク溶接では、有害な煙やガスが発生するため、換気をしっかり行い、作業中のガス管理を徹底することが大切です。
溶接作業における重要な注意点と質の向上への取り組み
溶接作業の質を確保し、事故を未然に防ぐためには、作業環境や使用材料、適切な手法を選択することが不可欠です。
特に溶接時の安全対策として、耐火性のある作業服、保護メガネ、溶接マスクの着用が求められます。
また、適切な材料の選定や溶接機器の点検を徹底することも、長期的な品質の維持につながります。
矢内精工(株)では、最新の溶接技術と高度な設備を駆使し、熟練の技術者が高品質で安全な溶接作業を提供しています。
溶接に関する悩みや疑問がある場合、どうぞお気軽にお問い合わせください。
私たちは、確かな技術でお客様のご期待にお応えします!