冷間鍛造と熱間鍛造、どちらを選ぶべきか悩んでいませんか?
この選択が、製品の精度、強度、コストに大きく影響することは、製造業に携わる技術者やエンジニアの方々ならご存知でしょう。
本記事では、精密部品製造に関わる方々に向け、それぞれの鍛造方法の特徴や利点を徹底解説します。
コスト削減や品質向上を目指す中小企業の経営者にも必見の内容です。
あなたの製品に最適な選択を見つけましょう!
冷間鍛造とは?

冷間鍛造は、寸法変化が少なく精密な加工ができるため、たとえばネジやボルトのような小型部品の大量生産に最適です。
従来の切削加工と比べて材料ロスが80%削減され、歩留まりが95%に達することもあります。
さらに、環境に優しいという点では、廃棄物がほとんど出ないため、年間数百トンの廃棄金属を削減でき、製造コストを20%以上低減することが可能です。
特徴と利点
- 寸法変化が少なく、精密な加工が可能
- 材料の無駄がなく、歩留まりが高い
- 小型部品の量産に最適でコストダウンが可能
- 廃棄物がほとんど発生しないため、環境に優しい
- 高精度な仕上がりで、後工程の削減が可能
冷間鍛造は、精密な加工に適しており、材料ロスが少ないため効率的な生産が可能です。
小型部品の量産やコスト削減、環境に優しい点が大きな利点です。
熱間鍛造とは?
熱間鍛造は、金属を約900°C~1,200°Cに加熱し、柔らかい状態で圧力をかけて成形する方法です。
複雑な形状や大型部品の加工に適しており、同時に金属の強度や靭性を向上させます。
特徴と利点
- 変形抵抗が小さく加工が容易
- 大型部品の成形に最適
- 複雑な形状を自由に成形可能
- 金属の強度・靭性を向上
- 鍛造と熱処理を同時に行い効率化
熱間鍛造は、大型部品や複雑な形状の成形に優れ、金属の強度や靭性を向上させます。
加工が容易で、耐久性が求められる製品に最適です。
冷間鍛造 vs 熱間鍛造!その違いは?

製品の精度やコスト、強度が決定要因となる鍛造法の選択は、技術者にとって非常に重要です。
高精度な加工が求められる場合には冷間鍛造が適しており、大型部品や複雑な形状が必要な場合には熱間鍛造が最適です。
それぞれの違いを詳しく見ていきましょう。
ワーク温度
熱間鍛造では、金属を高温(約900°C~1,200°C)で加工しますが、冷間鍛造は常温で行います。
この違いが成形の柔軟性に大きく影響します。
寸法精度
冷間鍛造は、常温で行うため寸法精度が非常に高く、精密部品の製造に向いています。
膨張や収縮が少ないため、後加工も少なく済みます。
一方、熱間鍛造では高温で金属を加工するため、金属が膨張・収縮しやすく、寸法精度がやや劣ることがあります。
ワークサイズ
冷間鍛造は、小型で精密な部品の大量生産に適しており、材料の無駄も少なく効率的です。
これに対し、熱間鍛造は、金属を高温で柔らかくして加工するため、大型部品や複雑な形状の成形が得意で、特に強度が求められる部品に適しています。
ネットシェイプとニアネットシェイプ
冷間鍛造は、精度の高いネットシェイプやニアネットシェイプ加工が可能です。
熱間鍛造では、追加加工が必要な場合が多いです。
ネットシェイプ技術とは、無加工で最終形状に近い部品を製造できる技術を指します。
これにより、追加加工を必要とせず、材料やコストの削減が可能です。
特に精密な形状が求められる部品の製造で強みを発揮し、効率性と品質の向上を実現します。
ニアネットシェイプは最終形状にほぼ近い形で製造し、追加加工を減らす技術。
用途の違い
熱間鍛造は、高い強度や耐久性が必要とされる大型部品に適しています。
たとえば、自動車の車軸や航空機の構造部品など、負荷の大きい部品にはこの加工法が理想的です。
一方、冷間鍛造は、精度が要求されるネジやボルト、電子機器の小型部品などの製造に最適!
高精度で複雑な形状が可能であり、材料の無駄も少ないため、コスト削減が可能です。
それぞれの鍛造法は、製品のサイズや精度、製造コストに応じて異なる特徴を持っています。
どちらの方法を選択すべきかは、具体的な製品の仕様や求められる性能によって決定されます。
矢内精工の鍛造技術
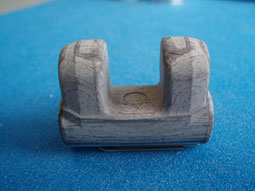
矢内精工(株)は冷間鍛造に特化しており、熱間鍛造は行っていません。
冷間鍛造の技術を活かし、ステンレス加工や厚板のブランク抜きなど、精密かつ高効率な金属加工を提供しています。
また、表面潤滑処理(ボンデ処理)も対応可能で、顧客のニーズに応じた柔軟な対応が特徴です。
矢内精工(株)の冷間鍛造技術は、コスト削減と高精度な仕上がりを実現し、多様な製品に対応しています。
冷間鍛造と熱間鍛造の選び方
冷間鍛造と熱間鍛造の選び方は、製品の用途や要件に応じて決まります。
精密さが求められる場合
冷間鍛造は、高精度が求められる製品に最適です。
特に、小型で複雑な形状の部品、例えば電子機器の微細なパーツや高精度な機械部品の製造に適しています。
冷間鍛造は常温で行われるため、加工中の寸法変化が少なく、細かいディテールを忠実に再現することができます。
また、後加工が少なく済むため、製造工程全体のコスト削減が可能です。
たとえば、ネジやボルトなど、寸法誤差が数ミクロン単位で許されない部品の大量生産には、この高精度な冷間鍛造が活躍します。
このような部品は、製品全体の品質に直結するため、冷間鍛造による精密加工が信頼されています。
大型部品や強度が重視される場合
熱間鍛造は、金属を高温で柔らかくしてから加工するため、大型部品や複雑な形状に最適です。
さらに、強度や靭性を向上させるため、耐久性が必要な部品に向いています。
冷間鍛造を選ぶべき場合
- 高精度が求められる
- 小型部品の大量生産が必要
- 環境に優しい製造が重要視されている
熱間鍛造を選ぶべき場合
- 大型で複雑な形状の部品が必要
- 強度や靭性の強化が求められる
このように、製品の仕様や製造条件によって、それぞれの鍛造方法が最適な選択となります。
冷間鍛造と熱間鍛造の選択ポイント!どちらを選ぶべきか?
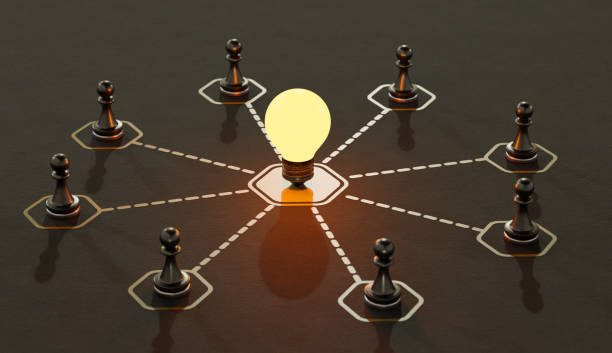
冷間鍛造と熱間鍛造を選択する際には、製品の特性や製造の目標に応じた判断が必要です。
どちらの方法が最適かを決めるためには、次のポイントを考慮することが重要です。
製品の精度
高精度が求められる場合には、冷間鍛造が最適です。
冷間鍛造は、寸法変化が少なく、切削加工の必要がないため、後加工を削減でき、コスト削減にもつながります。
製品のサイズと複雑さ
大型部品や複雑な形状が必要な場合、熱間鍛造が適しています。
高温で金属を柔らかくすることで、複雑な形状の成形が可能となり、強度も向上します。
コスト効率と材料の無駄
冷間鍛造は材料の無駄が少なく、歩留まりが高いため、効率的な生産が可能です。
環境に優しい製造プロセスも実現でき、コストパフォーマンスに優れています。
強度と靭性
強度や靭性が求められる部品には、熱間鍛造が適しています。
特に、金属の機械的特性を向上させるためには、熱間鍛造が効果的です。
適切な選択を今すぐ!
冷間鍛造と熱間鍛造の違いを理解し、製品のニーズに応じた適切な方法を選択することで、製造コストを削減し、品質を向上させることが可能です。
矢内精工(株)の冷間鍛造技術を最大限に活用して、効率的で高品質な製品づくりを実現しましょう。
よくある質問Q&A
Q1: 温間鍛造と熱間鍛造の違いは何ですか?
A: 温間鍛造は300〜900℃の範囲で行われ、熱間鍛造は1000〜1250℃の高温で行われます。温間鍛造は冷間鍛造より成形が容易で、熱間鍛造に比べ寸法精度が高いですが、強度や靭性は熱間鍛造の方が優れます。
Q2: 冷間鍛造の欠点は何ですか?
A: 冷間鍛造は常温で行うため、材料の可塑性が低く、複雑な形状や細部を持つ部品の成形が難しい場合があります。
Q3: 冷間プレスと熱間プレスの違いは何ですか?
A: 冷間プレスは高精度ですが加工が難しく、熱間プレスは柔軟で複雑な形状の成形に適していますが、精度が低くなることがあります。
最適な鍛造方法を今すぐ選び、製造効率を向上させましょう!
冷間鍛造と熱間鍛造の違いをしっかり理解することで、製造コストや製品の品質に大きな違いを生み出すことができます。
精密さや小型部品の大量生産を求める場合は冷間鍛造が最適ですし、強度や複雑な形状、大型部品が必要な場合は熱間鍛造が適しています。
矢内精工(株)の技術を活かし、適切な鍛造方法を選ぶことで、効率的かつ高品質な製品づくりが実現できます。
製品のニーズに合った選択を今こそ考えてみませんか?