冷間鍛造とプレス加工は、一見すると似ている加工方法に思われるかもしれませんが、実はそれぞれに独自の特長やメリットがあります。
あなたの製造プロセスにおいて、どちらを選ぶべきか迷っていませんか?
本記事では、冷間鍛造とプレス加工の具体的な違いを徹底解説し、どの場面でどちらの方法を選択するべきか、判断のポイントをお伝えします。
効率的で品質の高い製造を実現するためのヒントが満載です。
冷間鍛造やプレス加工に携わる方にとって、業界の最前線で役立つ情報をお届けしますので、ぜひ参考にしてください!
冷間鍛造とプレスの違いを理解することで選択肢を広げる
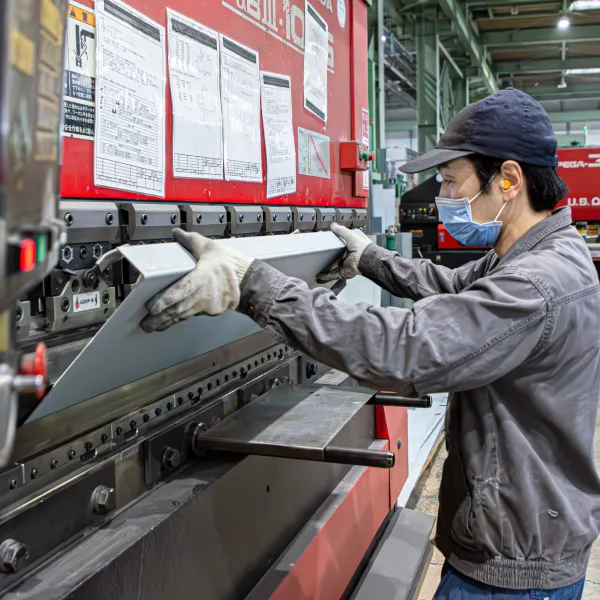
冷間鍛造とプレスの違いを正しく理解することで、製品の特性や生産性を最適化できる選択肢が広がります。
ここでは、なぜ両者の違いを理解することが重要なのかについて解説し、適切な加工法を選択するための知識を深めていきます。
冷間鍛造とプレスの基本的な違い
冷間鍛造とプレス加工は、どちらも金属を成形するための技術ですが、それぞれに特有の大きな違いがあります。
これらの違いを理解することで、最適な加工方法を選択し、生産性や品質を向上させることが可能です。
材料の厚さが異なる
冷間鍛造では、ビレットと呼ばれる厚い金属を使用します。
この厚い材料を強い圧力で押しつぶしながら形状を作り出すため、強度の高い部品が必要な製品に適しています。
一方、プレス加工では、ブランクという比較的薄い板材を用いています。
このブランクをコイル状に巻き、レベラーを通して材料を平らにしてから成形します。
材料の厚さが異なるため、冷間鍛造は強度重視、プレス加工はコスト効率重視の場面で選ばれることが多いです。
使用される材料の違い
冷間鍛造とプレス加工で使用される材料にも大きな違いがあります。
プレス加工では、SPCC材と呼ばれる軟鋼が使用されることが一般的です。
この材料は成形性に優れ、加工しやすいという特性を持っています。
そのため、複雑な形状を簡単に作り出すことが可能です。
冷間鍛造では、SWCH材のような炭素鋼が多く用いられます。
この材料は高い強度と硬度を持ち、強度が要求される部品の製造に適しています。
熱処理の有無
冷間鍛造では、材料を加工する過程で加工硬化が生じ、部品の内部に応力が蓄積されます。
これを取り除くためには、焼鈍(焼なまし)という熱処理が必要になります。
熱処理を行うことで材料の靭性を向上させ、耐久性のある製品を作り上げることが可能。
一方、プレス加工にはこの熱処理が不要で、短期間で大量に部品を製造することが可能です。
材料と製品の板厚の変化
冷間鍛造とプレス加工では、材料と製品の板厚の変化にも違いがあります。
- 冷間鍛造では、厚い板材を圧縮して形を成形するため、材料と製品の板厚に大きな差が生じます。材料が潰されることで、より複雑で強度の高い部品を作ることができるのが特徴です。
- 一方で、プレス加工は基本的に材料の厚さを変えることなく成形するため、製品の厚みは材料のそれとほぼ変わりません。特に薄い板材を使用する場合には、成形後の製品でも同じ厚さが保たれます。
冷間鍛造とプレスの基本的な違いのまとめ
冷間鍛造とプレス加工はそれぞれ異なる特徴を持っており、どちらを選ぶかは製品の要求される強度やコスト、作業環境に応じて異なります。
冷間鍛造は強度と耐久性を重視する部品に最適であり、プレス加工は大量生産や成形の効率性を求める場合に適しています。
最適な加工方法を選ぶことで、製造の効率と品質が大きく向上します。
冷間鍛造のメリット
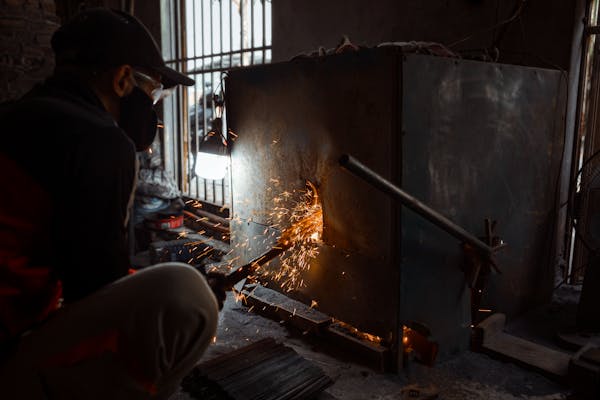
冷間鍛造には、多くの製造業で利用される理由がいくつかあります。
それは、加工の自由度の高さや強度の向上、そして高速な加工スピードです。
メリット1:加工の自由度が高い
冷間鍛造の大きな強みの一つは、その加工の自由度の高さです。
これは、特に複雑な形状の部品や細かいディテールを持つ部品の製造において、非常に有効です。
- 室温で加工されるため、材料が過度に熱変形することなく、形状の変化を細かく制御できる。
- 部品のデザインにおいて、皿モミやザグリなどの複雑な断面形状や、材料の厚みの変化にも対応可能。
自動車部品や精密機器のコンポーネントにおいては、高精度かつ高品質な製造が可能なため、設計の自由度が非常に高まります
メリット2:強度が高くなる
冷間鍛造の重要なメリットは、加工された部品の強度が向上することです。
冷間鍛造は、材料の結晶構造を変化させ、金属内部の結合を強化することで、部品の硬度や引張強度が向上します。
- このプロセスにより、製品の耐久性が高まり、長期にわたって信頼できる部品が得らる。
- 自動車のエンジン部品や航空機のコンポーネントなど、機械的ストレスが大きい部品に特に有効。
これにより、高耐久性を要求される用途に最適な製品を提供できます。
メリット3:加工スピードが速い
冷間鍛造は、加熱や冷却の工程が不要なため、部品の製造スピードが非常に速いです。
そのため、製造サイクルの短縮が可能になり、効率的な大量生産が実現します。
- 室温での加工により、生産時間の短縮が図れ、短期間で大量の部品を生産することができる。
- 特に自動車産業などでは、高速プレス機械を使って大量生産を実施する際に、一貫性と高品質を保ちながら、短時間で製品を供給できる。
また、加工スピードの速さは、単に生産性を高めるだけでなく、コスト削減にも繋がります。
製造効率が向上することで、労働時間や設備の運用コストが抑えられ、経済的なメリットも生まれます。
冷間鍛造のプロセスとメリット
冷間鍛造のメリットは、材料の強度を保ちつつ形状を精密に加工できることです。
以下の工程で行われます。
- ビレットの準備: 厚い金属を加圧する前に切断。
- 鍛造: 金型を使い、ビレットを圧縮して目的の形状に加工。
- 仕上げ処理: 焼鈍などの熱処理を行い、硬化を防ぎつつ仕上げる。
冷間鍛造は強度を高めるため、自動車や航空機産業において不可欠な技術です。
プレス加工の特徴と利点

プレス加工は、ブランクと呼ばれる薄い材料を使い、コスト効率の良い大量生産が可能です。
主に以下の工程で行われます。
- ブランク準備: 薄い板材を準備し、レベラーを通して均一化。
- プレス成形: 材料に圧力をかけ、金型を使って形状を作り出す。
- 後加工: 打抜きや曲げ加工を行い、最終製品に仕上げる。
プレス加工は、家電や建築部品など、多様な製品に利用されています。
なぜこの材料が選ばれるのか?
冷間鍛造では、材料の強度が非常に重要であるため、硬度の高い炭素鋼が選ばれます。
一方で、プレス加工では成形性を重視するため、軟質の材料が多用されます。
各材料の選択は、最終製品の用途に合わせて行われます。
冷間鍛造とプレス加工のデメリットとは?
加工方法の選択に際して、デメリットも考慮する必要があります。
- 冷間鍛造のデメリット: 高度な技術力と専用設備が必要なため、初期コストが高くなることがあります。
- プレス加工のデメリット: 薄い材料しか扱えないため、製品の強度が制約されることがあります。
矢内精工の強みを生かす冷間鍛造とプレス加工の選択肢
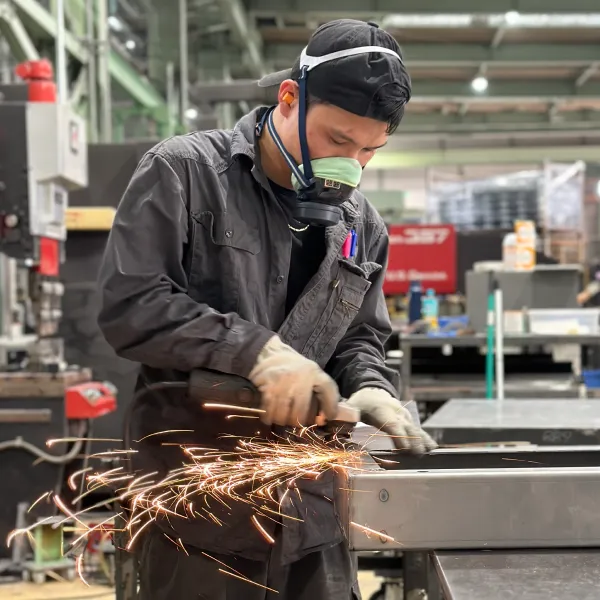
矢内精工(株)では、冷間鍛造とプレス加工の両方を活用して、高精度かつコスト効率の良い製品を提供しています。
- 金型技術: 高精度な金型を使用することで、耐久性と精度を両立しています。
- 材料選定: それぞれの加工方法に最適な材料を厳選し、品質を保証します。
よくある質問
Q: 鍛造プレス機と板金プレス機の違いとは?
A: 鍛造プレス機は、厚いビレット(原材料)を使用して高い圧力をかけて部品を成形するのに対し、板金プレス機は薄いブランク(金属板)を用いて主に形を作ります。鍛造は強度を高めるのに適しており、板金プレスは薄い部材の大量生産に向いています。
Q: プレス加工と冷間鍛造の使い分けは?
A: プレス加工は、薄い材料を効率的に大量生産するのに適しています。一方、冷間鍛造は、部品に高い強度が求められる場合に最適です。冷間鍛造は材料の密度を上げ、強度と耐久性を向上させる特長があります。
冷間鍛造とプレス加工の違いを理解して選択するポイント
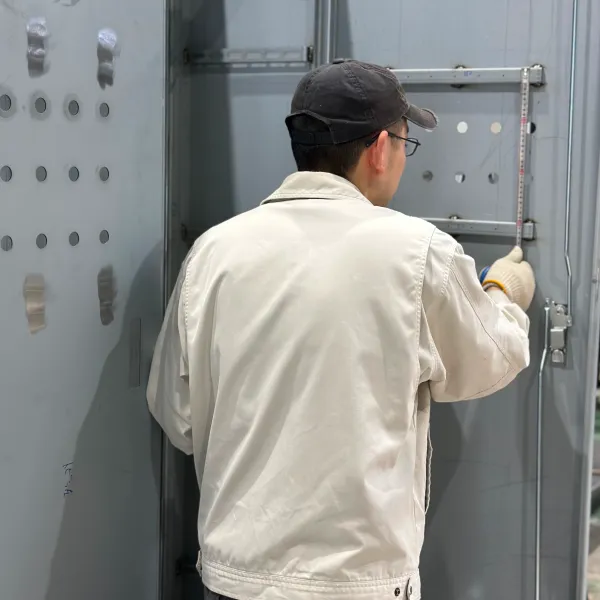
冷間鍛造とプレス加工の違いを理解し、どちらを選ぶべきかは、製品の形状やサイズ、生産量、コストといった要素に基づいて判断することが重要です。
以下は、それぞれの選択ポイントについて詳しく説明します。
製品の形状とサイズ
冷間鍛造は、小型で複雑な形状の製品に向いています。
冷間で材料を圧力成形するため、精密な寸法が求められる製品や強度が必要な部品に適しています。
特に自動車や航空機部品など、高精度が必要な分野で多く採用。
一方、プレス加工は、薄い金属板(板金)を使用し、形を成形するための加工です。
大量生産に適しており、シンプルな形状の製品に向いています。
例えば、家電製品の外装部品や、金属板を曲げたり打ち抜いたりする工程が求められる製品がこの加工方法に適しています。
生産量
プレス加工は、大量生産に非常に効率的です。一度金型を作成すれば、短時間で大量に製品を作り出せます。
これは、大規模な生産ラインや需要の多い製品に適しています。
一方、冷間鍛造は、一般的に中小規模の生産向けです。
プレス加工ほどの高速生産は得意ではありませんが、その代わりに高い精度と強度が要求される場合に向いています。
品質重視の製品に適した方法です。
コスト
コスト面では、冷間鍛造は材料の無駄が少ないため、材料コストの削減が可能です。
削り屑などの廃棄物が少なく、効率的に材料を使うことができるため、コストパフォーマンスに優れています。
ただし、冷間鍛造は成形する際に高い圧力がかかるため、金型の摩耗が早い場合もあります。
一方、プレス加工は、初期費用が高くなります。
金型の製作費やプレス機の導入コストがかかるためですが、大量生産を行う場合には、1つあたりのコストが抑えられるため、トータルコストが低くなります。
初期投資が大きくても、その後のランニングコストが低いのが魅力です。
冷間鍛造とプレス加工の違いを理解し、最適な加工法を選ぼう
冷間鍛造とプレス加工の違いを理解することで、製造効率と品質を最適化できます。
冷間鍛造は、強度が求められる小型部品に適しており、プレス加工は薄い金属板を使用した大量生産に向いています。
製品の形状や生産量、コストを考慮し、どちらの加工法が最適かを選ぶことが重要です。
矢内精工((株)では、これら2つの加工技術を駆使し、最高品質の製品を提供しています。
最適な加工法を選びたい方は、ぜひ当社にご相談ください。