ステンレスは、その耐食性や強度の高さから、さまざまな分野で利用される金属材料の一つです。食品加工機械、建築、医療機器、化学プラントなど、幅広い業界で採用されており、その加工技術も日々進化を遂げています。特に溶接は、ステンレス加工において重要な役割を果たす技術の一つであり、適切な手法を選択しなければ品質や耐久性に影響を及ぼします。本記事では、ステンレス溶接の特徴や技術、注意点について詳しく解説していきます。
ステンレスの溶接の基本
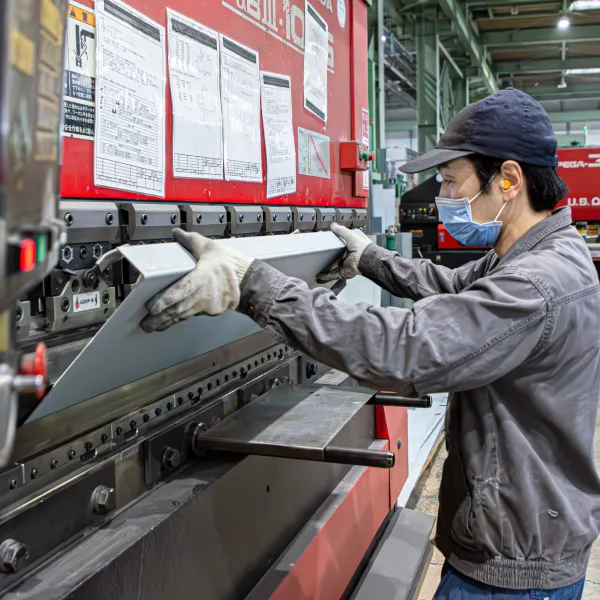
ステンレスは一般的な鉄鋼と比べると熱伝導率が低く、膨張係数が大きい特徴があります。そのため、溶接時には適切な熱管理が求められます。溶接方法によっては、熱影響部の変形やひずみが発生しやすいため、適切な施工が必要です。
ステンレス溶接にはいくつかの方法があり、それぞれの特徴を理解した上で最適な手法を選ぶことが重要です。主な溶接方法としては、TIG溶接(タングステン・イナート・ガス溶接)、MIG溶接(メタル・イナート・ガス溶接)、レーザー溶接、スポット溶接などがあります。
各種ステンレス溶接の種類と特徴
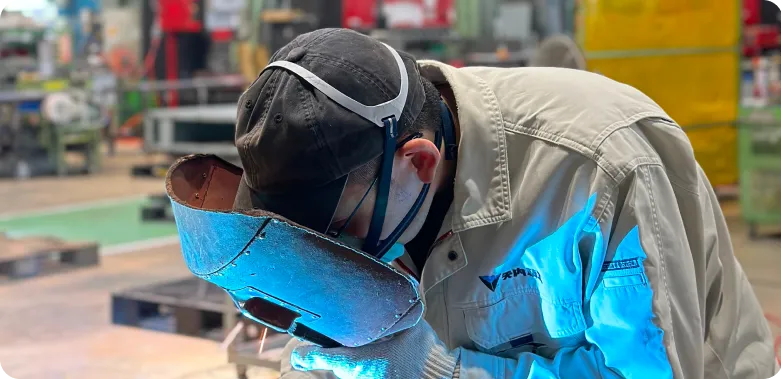
TIG溶接(Tungsten Inert Gas Welding)
TIG溶接は、ステンレスの溶接において最も一般的に用いられる手法の一つです。タングステン電極を使用し、不活性ガス(アルゴンやヘリウム)で保護しながら溶接を行うため、溶接部の品質が高く、精密な加工が可能です。また、スパッタ(溶接時に飛び散る金属粒子)が少なく、仕上がりが美しいのも特徴です。
TIG溶接は、特に薄板の溶接や高品質が求められる場面に適しています。しかし、溶接速度は比較的遅く、大量生産には向いていません。
MIG溶接(Metal Inert Gas Welding)
MIG溶接は、溶接ワイヤを自動的に供給しながら、アーク放電によって溶融させる方法です。不活性ガスを使用して大気中の酸素や窒素を遮断するため、比較的安定した溶接が可能です。TIG溶接と比較すると、作業スピードが速く、大量生産に適しているのが特徴です。
ただし、MIG溶接はスパッタが発生しやすく、溶接部の仕上げ作業が必要になる場合があります。また、厚板の溶接には適していますが、薄板の溶接では熱影響が大きくなりやすいという課題もあります。
レーザー溶接
レーザー溶接は、高エネルギーのレーザービームを照射して材料を溶融させる方法です。精密な制御が可能で、非常に細かい溶接線を作ることができるため、電子機器や医療機器などの分野で活用されています。また、熱影響が少なく、歪みが抑えられるため、薄板の溶接にも適しています。
ただし、設備のコストが高く、専用の機器が必要になるため、一般的な溶接作業には導入が難しい場合があります。
スポット溶接
スポット溶接は、電極を使用して局所的に大電流を流し、材料同士を瞬間的に溶接する方法です。主に自動車や家電製品の製造など、大量生産が求められる場面で使用されます。溶接速度が非常に速く、量産性に優れていますが、溶接の強度や精度には限界があります。
ステンレス溶接の注意点
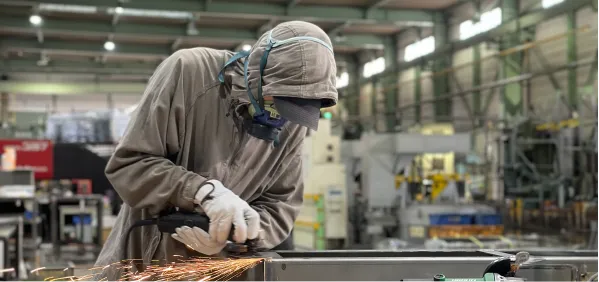
ステンレスの溶接を行う際には、いくつかの重要なポイントを押さえておく必要があります。
まず、溶接時の熱管理が重要です。ステンレスは熱による膨張が大きいため、熱影響部が変形しやすい傾向にあります。特にTIG溶接やMIG溶接では、適切な電流設定や冷却方法を工夫することで、ひずみを抑えることができます。
また、酸化防止も重要です。ステンレスは酸化しやすく、溶接後に酸化スケールが発生すると、耐食性が低下してしまいます。溶接後には酸洗いやパッシベーション処理を行い、表面を清浄に保つことが求められます。
さらに、適切なフィラー材の選定も欠かせません。ステンレスの種類によって、使用するフィラー材が異なるため、溶接部の品質や強度を確保するために適切な材料を選ぶことが重要です。
まとめ
ステンレスの溶接は、素材の特性を理解し、適切な方法を選択することが品質や耐久性を向上させる鍵となります。TIG溶接は高品質な仕上がりが求められる場面に、MIG溶接はスピードと量産性が必要な場面に、レーザー溶接は精密な加工が必要な場面に、それぞれ適しています。さらに、熱管理や酸化防止、適切なフィラー材の選定を行うことで、より高品質なステンレス溶接が実現できます。
今後も技術革新が進む中で、新たな溶接技術の開発や改善が期待されており、ステンレス加工の分野において溶接の重要性はますます高まるでしょう。適切な溶接技術を選択し、最適な加工を行うことで、より高品質な製品の提供が可能となります。