切削加工に欠かせない課題の一つが「切粉」の処理です。
切粉が加工精度や作業効率に影響を及ぼすだけでなく、適切に管理しないと環境負荷にもつながるため、各企業が注目すべきテーマとなっています。
さらに、切粉リサイクルを取り入れることで、コスト削減や環境配慮を実現する可能性があります。
本記事では、切削加工における切粉の影響とその管理方法を解説し、企業が効率性と環境配慮を両立するためのヒントを提供します。
切削加工で発生する切粉の処理方法とは?
切粉(きりこ)は切削加工の過程で避けて通れない存在です。
適切に処理しないと、製品品質の低下や生産効率の悪化につながる可能性があります。
ここでは、切粉が引き起こす問題とその対策について、分かりやすく解説します。
切削加工による切粉処理の重要性と課題
切削加工の現場では、切粉は避けて通れない存在であり、その処理方法が製品品質や生産効率に大きく影響します。
適切に処理されない切粉は、製造工程でトラブルを引き起こし、結果的にコストの増加や作業効率の低下につながる可能性があります。
そのため、効果的な管理方法の導入が重要です。
以下では、切粉処理の具体的な課題とその重要性について解説します。
ポイント
切粉によるトラブルを未然に防ぐことで、生産効率を向上させ、品質不良のリスクを低減できます。以下にトラブル例を示します。
トラブル例
- 切粉が工具やワークに巻きつき、製品を傷つける
- 穴加工時に切粉が詰まり、ドリルの折損を引き起こす
- チャックやシャンクに切粉が噛み込み、加工不良や停止が発生
切粉が原因で発生する具体的なトラブル
加工面の損傷: 長い切粉が工具や加工物に巻き付き、加工面を傷つけることがあります。
工具寿命の低下: 切粉が工具に絡むことで、工具の摩耗や折損を早めてしまいます。
切粉の巻き付きによる事故: 切粉が作業者に巻き付き、怪我の原因となることがあります。
次に効果的な切粉処理方法についてみていきましょう。
効果的な切粉処理方法

効果的な切粉処理方法のポイント
工具や加工条件を最適化することで、切粉処理を改善し、稼働停止時間を減少させる。
チップブレーカ(切削工具の刃先近くに設けられた溝や形状)の活用
・切粉を効率的に分断し、工具やワークへの巻き付きを防止
・ワーク材質や切り込み量に応じた選定が重要
チップブレーカの選定基準や使用例についてはこちらをご覧ください。
切削加工中の工具の移動経路の工夫
・加工経路を変更し、切粉の排出を促進
切粉が工具やワークに絡まるのを防ぐため、切削経路を工夫して切粉の流れをスムーズにします。特に、穴加工や複雑な形状加工では経路設計が重要です。
・揺動切削(スイング加工)の活用
揺動切削は、工具の微振動で切粉を自然に分断し、特に深穴加工や詰まりやすい環境で効果を発揮します。
クーラントの使用
・高圧クーラントで切粉を洗い流す
高圧クーラントは、切粉を迅速に洗い流し、巻き込みや詰まりを防いで加工精度を保ちます。
・センタースルー方式の活用(特に穴加工に有効)
「センタースルー方式」により、穴内部の切粉詰まりを防ぎ、ドリル折損のリスクを低減しつつ深穴加工が可能です。
・振動を利用した「揺動切削」機能の併用
クーラントと揺動切削を組み合わせると、切粉が効率的に分断され、排出がスムーズになります。この技術は、切粉が詰まりやすい加工で特に効果的です。
切削条件の最適化

切削条件を最適にするポイント
加工効率と品質のバランスを取りつつ、切粉の発生をコントロールすることが重要です。そのためには、以下のポイントに注意して加工条件を設定しましょう。
- 主軸回転数: 高速回転で理想的な流れ型切粉を生成しやすい
- 送り速度: 適切な速度設定で切粉排出をスムーズにする
- 切り込み量: チップブレーカを効果的に機能させるための調整が必要
切粉管理がもたらすメリット
切粉管理を徹底することで、企業に次のような利点をもたらします。
メリット
- 製品品質の向上: 表面仕上げ精度の改善
- 生産性向上: チョコ停や工具破損のリスクを軽減
- コスト削減: 切粉トラブルによる再加工や工具交換の頻度を削減
切粉処理の最新技術
最新技術を取り入れることで、競争力を高め、企業の信頼性向上につながります。
・自動切粉除去システムの導入
・AIを活用した工具寿命管理
・環境配慮型のリサイクル切粉処理
切粉の処理方法まとめ |
---|
・切粉トラブルの防止策を導入することで、生産効率と製品品質を向上 ・ 主な対策: チップブレーカの活用、加工経路の工夫、高圧クーラントの使用 ・ 最新技術の導入(AIや自動処理システム)で効率性と環境配慮を実現 |
切粉処理の効率化に向けた最新技術の導入をご検討中の企業様は、ぜひ矢内精工(株)までご相談ください!
切削加工における切粉管理で環境配慮とコスト削減を両立する方法
切粉リサイクルは、企業のコスト削減だけでなく、環境負荷の低減にも寄与する重要な取り組みです。
以下に、切粉リサイクルの具体的な実現方法とその効果を説明します。
切粉リサイクルの実現性と期待される効果
近年、切粉リサイクル技術が進化し、環境負荷を抑えながらコスト削減を図る取り組みが拡大。
特に、水溶性油を含むアルミ切粉の脱油技術は、高脱油率を実現し、切粉や切削油の再利用を可能にします。この再利用により、コスト削減と環境負荷軽減に大きく貢献しています。
切粉リサイクルのメリット
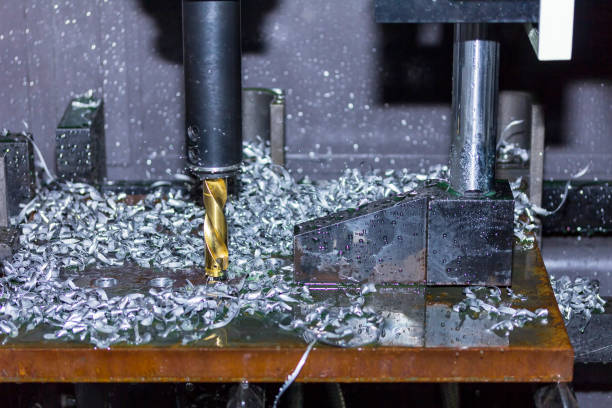
切粉をリサイクルすることで、以下のような効果が期待されます。
コスト削減
・素材費の低減: 切粉を再利用することで、新素材の購入コストを削減
・運搬費用と保管スペースの節約: 工場内で切粉処理を行うことで、廃棄物の運搬費用が削減
環境負荷の軽減
・温室効果ガス(CO2)の削減: リサイクルを通じて原材料の製造工程を削減
切粉リサイクルを効率化する技術
切粉管理の最新技術では、脱油用遠心分離機による水溶性油の効率的な除去が注目され、資源の再利用とコスト削減が可能です。
また、自動化技術と環境配慮型クーラントにより、省エネ・低コスト運用と環境負荷の軽減を実現しています。
切削加工における切粉の再利用事例
切粉の再利用は、製造業でコスト削減や環境負荷軽減を目指す上で重要な取り組みです。
この表で、切粉の再利用方法とそのメリットを解説します。
切粉の種類 | 再利用方法 | 活用事例 | ポイント |
アルミニウム | 溶解して新たな製品の原材料に使用 | 自動車部品、建材、飲料缶 | 水溶性油の除去が重要。脱油用遠心分離機を活用 |
鉄・ステンレス | 圧縮・固形化して溶解炉で再利用 | 鋼材、建築資材 | 油分・異物の除去が品質確保に必須 |
真鍮・銅 | 精錬して純度を高め、電線や部品の素材に再利用 | 電気製品、配管部品 | 迅速な処理で酸化防止を図る |
切粉の再利用はコスト削減と環境配慮の両立を実現する重要な取り組みです。それぞれの素材に適した方法を採用し、リサイクルの可能性を最大限に活用しましょう。
冷間鍛造による切削加工の最小化:効率と環境配慮の両立
矢内精工(株)では、冷間鍛造技術を活用して、円筒状の部品を最初から目的に近い形状に成形します。
この技術により、通常必要とされる研削加工を最小限に抑えることが可能です。
研削加工を最小限とは?
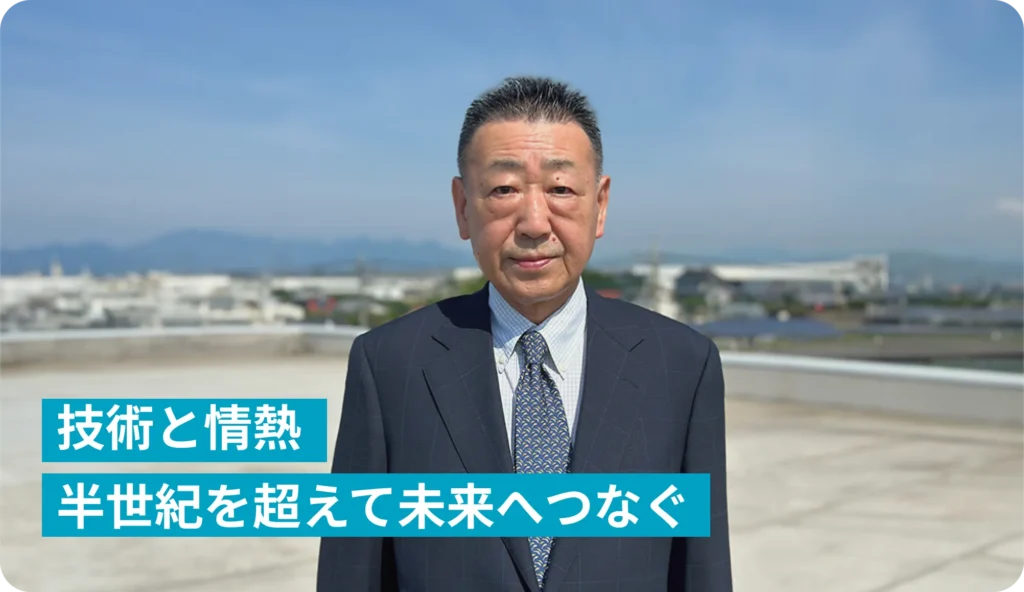
研削加工を最小限にするとは、部品の外側、具体的には円筒の側面部分に対する削りの工程をできるだけ減らすことです。
通常必要とされる研削加工も、矢内精工(株)の冷間鍛造技術により、初期段階から高精度な形状を実現します。この技術により、以下の効果が得られます。
・後工程での切削量を削減
初期段階から高精度に仕上げることで、研削加工を最小限に抑え、切粉の発生を減少。
・製造時間の短縮とコスト削減
削量の減少で加工時間が短縮し、工具寿命の延長や材料ロスを軽減。
・調整加工の必要性を最小化
冷間鍛造技術により高精度な部品が製造可能となり、調整作業の手間を大幅に削減。
これらのメリットを活かし、矢内精工(株)は効率的で環境に優しい生産を実現し、高品質な製品でお客様のニーズに応えています。
まとめ:切削加工と切粉管理で競争力を高めましょう!
切削加工における切粉の管理と再利用は、品質向上、コスト削減、環境配慮を実現するために欠かせない要素です。
そこで、矢内精工(株)では、冷間鍛造技術をはじめとした高度な加工技術を活用し、効率的かつ環境に優しい生産プロセスを提供しています。
これらの取り組みにより、切粉の発生を抑えつつ、生産効率向上や廃棄コスト削減、リサイクル推進が可能です。
ぜひ、矢内精工(株)までお問い合わせいただき、最適な加工方法と切粉管理の実現に向けた一歩を踏み出してください。